小さなロスを潰し『もっとラクに働けて、仕事に集中できる』町工場へ 有限会社今村精工 今村清孝さん
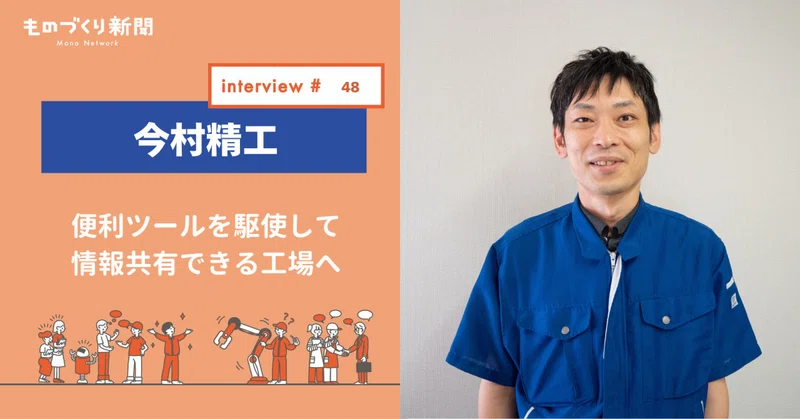
編集部は長野県飯田市にある有限会社今村精工を訪ねました。今村精工はマシニングセンタやNC旋盤加工機を用いた精密部品加工を行なっています。今回お話を伺ったのは、専務取締役の今村清孝(いまむら きよたか)さんです。
編集部が注目したのは今村精工のIT・IoT化についてです。今村さんが入社された2011年頃から取り組み始め、様々なツールを活用しながら、『もっとラクに働けて、仕事に集中できる』そんな町工場を目指しています。
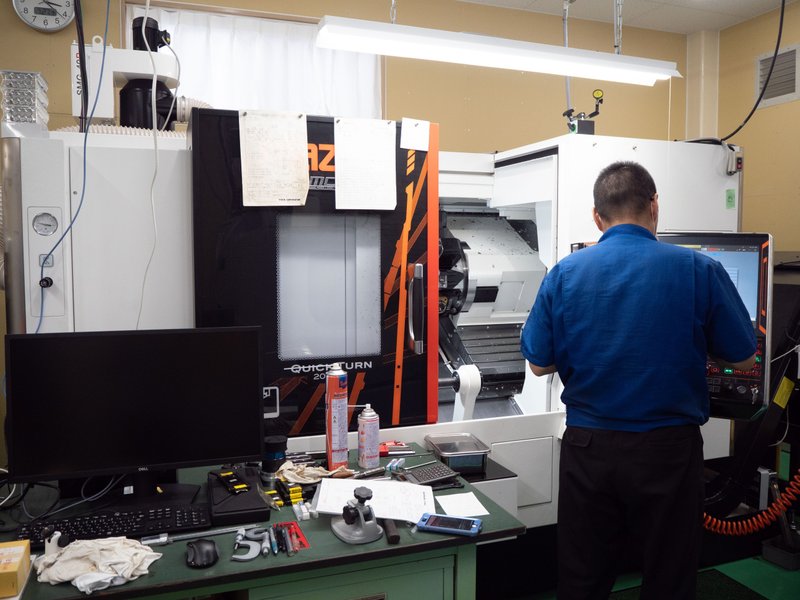
近年、IT・IoT化に取り組む町工場は増加しています。2022年版ものづくり白書によると『ものづくり工程・活動においてデジタル技術(ICT,IoT,AIなど)を活用している企業は全体の67.2%』といわれています。(参考文献:2022年版ものづくり白書第4章)
IT・IoTを活用した町工場とは一体どんな町工場なのでしょうか?
有限会社今村精工 今村清孝さん
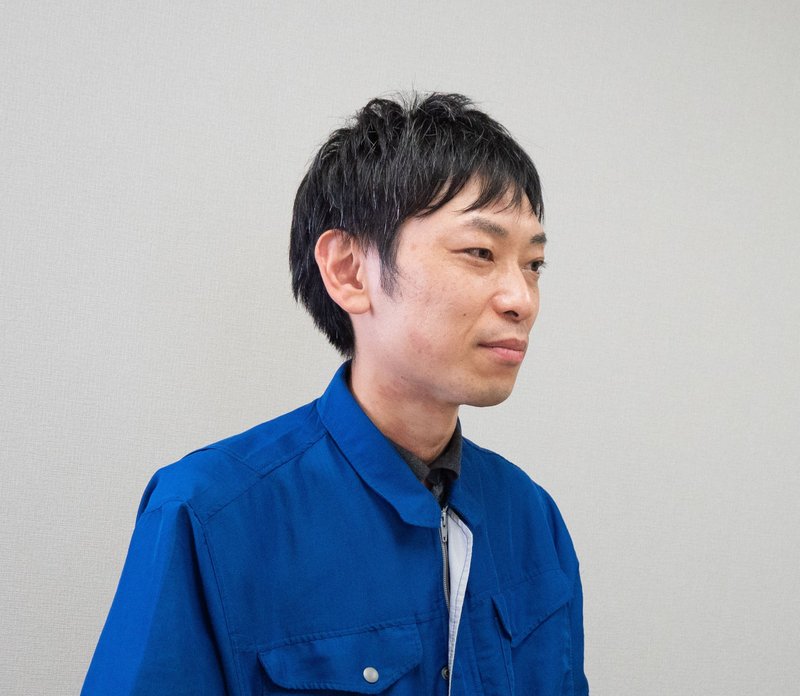
ーー子供の頃、家業である今村精工はどんな存在でしたか?
ーー当時はどのような部品を製造していましたか?
カメラなどの光学系の部品や、時計の部品など精密部品を製造していました。社長や社員が機械に部品をセットして、パートの女性の方々が量産していくスタイルだったと聞いています。
ーー今村さんは将来今村精工で働くことを考えていましたか?
家族全員が今村精工で働いていたので、小さい頃は「いつか自分もここで働くのかな」というある種疑問のような気持ちがありました。でも、働きたいと思ったことは一切ありませんでした。
ーー高校や大学時代はいかがでしたか?
継ぐという選択肢はなかったですね。父親から「戻ってきてほしい」とストレートに言われたこともありませんでした。冗談のような感じで「ここ(今村精工)があるからな」と言われたことはありましたが、真剣に話し合うことはなく、大学卒業後は企業に就職しました。
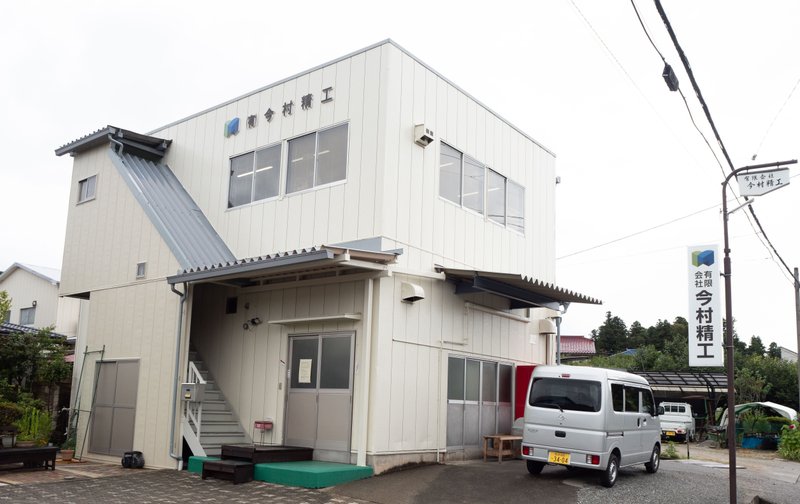
ーー大学卒業後はどのようなお仕事をされていたのですか?
実は製造業の仕事なんです。就職活動の時に、ITか製造業か2つの選択肢で迷っていました。情報系の大学で学んだことを活かせる仕事はIT系やシステムエンジニアですが、製造業にも関心があったのです。やはり育ってきた環境の影響もあったのかもしれないですね。ITと製造業の2軸で就職活動をした結果、長野県内の製造業に入社しました。入社して、まずは現場だなと言われマシニングセンタを担当しました。
ーー今村精工とかなり近い仕事ですよね。
そうです。でも、中学生くらいからは実家の工場に入ることはなかったので、機械を見たことすらありませんでした。どんな機械なのかもさっぱりわかりませんでした。
ーーご両親はどんな反応でしたか?
ちょっとびっくりしていたと思います。父からは「うちでも役に立つぞ」と言われました。
ーー実際仕事をしてみていかがでしたか?
難しくて毎日緊張の連続でした。先輩方は職人気質で、見て覚えるという感じです。感覚的な部分も多く、とにかく必死でした。ただ、その一方で、仕事を覚えていくうちに、徐々に物足りなさを感じるようになったんです。
ーーどんな部分に物足りなさを感じるようになったのですか?
展示会に足を運ぶと、最新の機械を使った加工やCAD・CAMを活用した機械加工の世界があることを知り、興味を持ちました。新卒で入社した会社には、そういった機械はあまりなかったため、思い切って東京の町工場に転職することにしました。
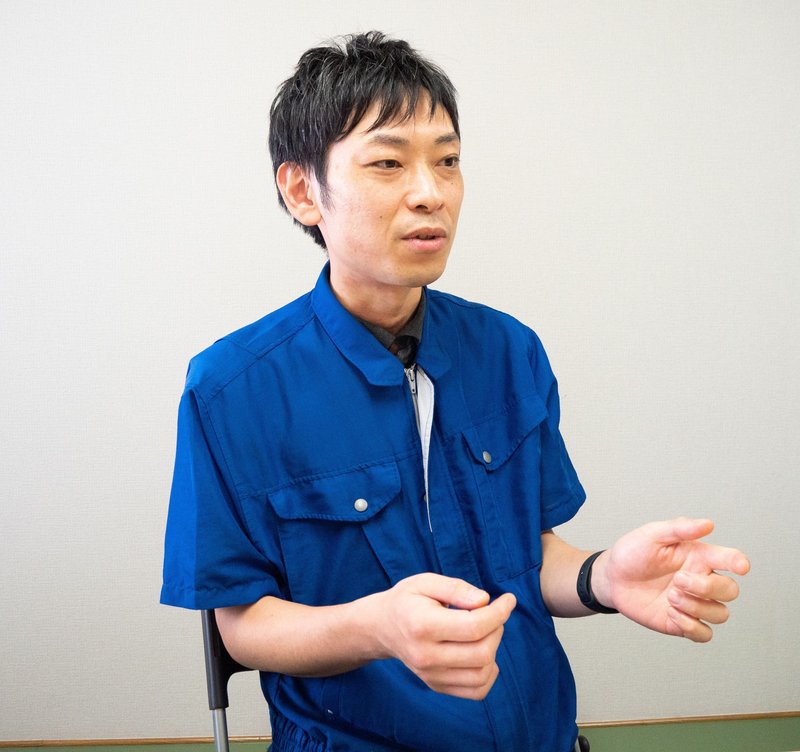
ーー思い切りましたね。東京の町工場を選んだ理由は何だったのでしょうか?
東京の町工場を特集している雑誌を読んだ時に、その会社の社長のインタビュー記事を見つけました。CAD・CAMは当然のこと、工場内のネットワークを整備してデジタルに対応しながらものづくりしている様子が書かれていて興味を持ちました。ホームページを見ると求人が出ていたので、応募して入社することになりました。
ーー転職先ではどんな仕事をされていたのですか?
その会社は主に試作品の加工・製造を行なっていました。私は入社してすぐに自分でプログラムを作り、加工して検査する一連の流れのほとんどを1人で担当することになりました。憧れの環境ではありましたが、仕事はすごく厳しかったです。でも設備投資は惜しまない会社だったので、最新の機械を使った加工も経験できて、大変でしたが本当に鍛えられました。
ーーそして、その次に入社されたのが今村精工でしょうか?
そうです。今村精工に入社しようと考えたのは2011年の東日本大地震がきっかけでした。実は地震があった次の日に結婚式を予定していたのですが、式は中止になり夫婦一緒に心身ともに参ってしまいました。個人的には激務による負担もあり、それがきっかけで転職を考えました。
ーー転職を考えた時に今村精工という選択肢が出てきたのでしょうか?
はい。妻に「実家に戻ってもいいんじゃない?」と言われたことが決め手です。父に相談すると、ちょうど「複合加工機の導入を決めたんだが、このタイプの機種を扱える人がいないからこれを機に戻ってこないか?」と言われました。狙ったわけではないのですが、タイミングが良かったのだと思います。私はそれまでマシニングセンタ(フライス削りや切削など多種類の加工ができる工作機械)や5軸加工機を使ってきた経験があったので、役に立てるかもしれないと思い決断しました。
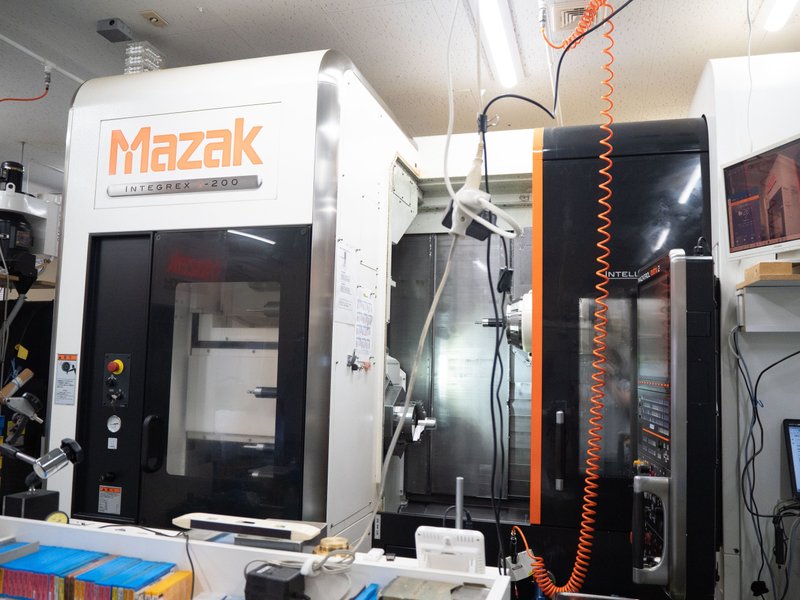
工程は作業者が管理していたため、全体が見えていなかった
ーー久しぶりに今村精工の工場に入った時はいかがでしたか?
どんな目で見られるんだろうとすごく心配していましたが、温かく受け入れてもらってほっとしたのを覚えています。
仕事に関しては、それまでマシニングセンタをメインでやってきたため、旋盤加工は未経験でした。複合加工機を使いこなすためには旋盤加工を覚える必要があり、教えてもらいながら試行錯誤してコツを見つける日々でした。
ーー入社した時の工場の印象はどうでしたか?
はじめは口にしませんでしたが、変えていきたいと感じる部分は多々ありました。
まず、他の工場でよく見かけるような工程表がありませんでした。図面や納期などの情報はみんなそれぞれの紙やノートに書き込んで把握していました。中には壁掛けのカレンダーに記入している人もいて、情報共有するということがありませんでした。ひとりひとりが情報を持っている状態なので、製品の加工状況が知りたい場合はひとりひとりに聞いて回るしかなかったんです。
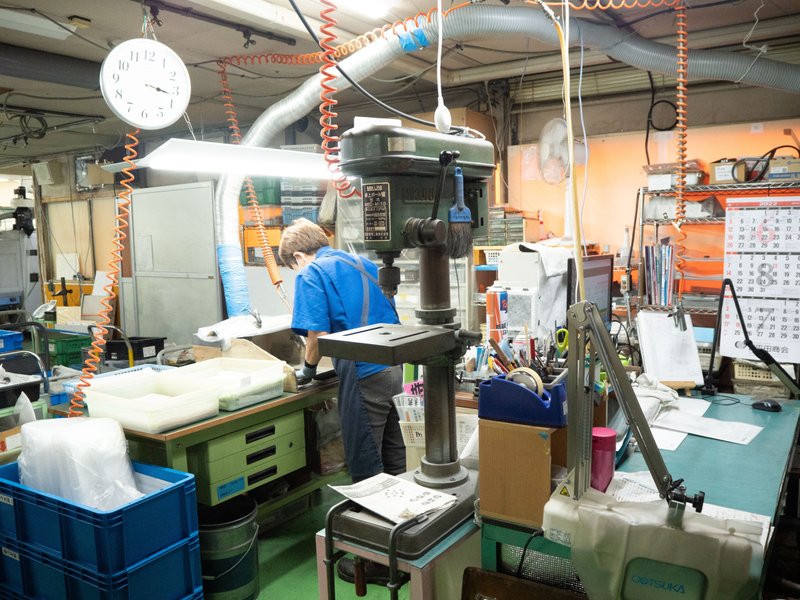
更に、事務所にしかパソコンがなく、あってもあまり活用できておらず、外部とのやり取りはほとんどがFAXでのやり取りでした。前職ではパソコンはもちろんのこと、ネットワークが整備されている環境が当たり前だったのでちょっと驚きました。
ーー自分が次に加工する製品が、今は誰の元にあるのかがわかりにくいということになりそうです。
そうです。あっちこっち歩きながら製品を探していました。当時納期管理をしていた生産事務の人が、工場内にいる人に片っ端から声を掛けて状況を把握していました。工程変更に伴いカレンダーの予定を書き換えているうちに、書いた本人でもよくわからなくなってきたこともありました。
ーーどのくらい工程が進んでいるかも把握しづらいですよね。
声を掛けて聞いて回るのは大変でしたが、それが当たり前でした。どこにも記録せず会話だけで話が進むことも多々あり、本当に把握しづらかったです。
パソコンやネットワークの便利さを知ってもらうことから始めた
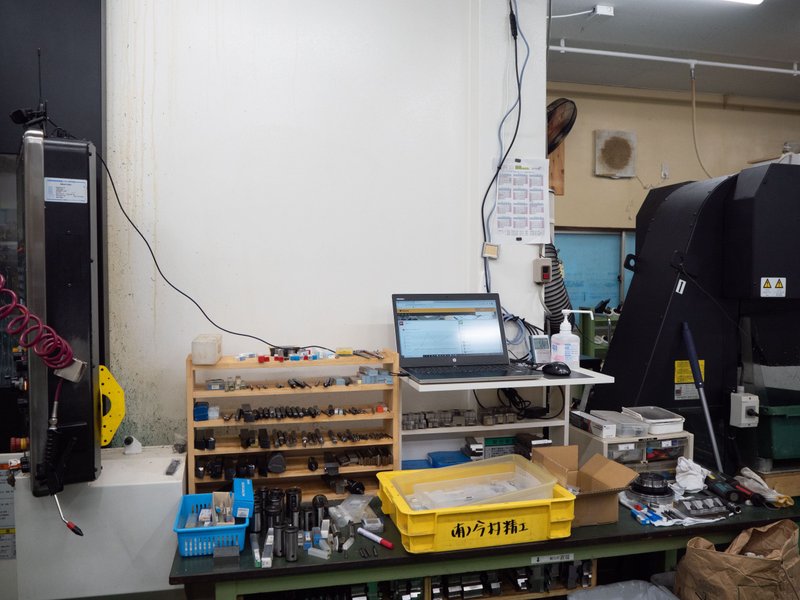
ーー課題に対して、今村さんは何から始めましたか?
まずは事務所で使っていた古くなったパソコンを新しいものに変え、更に台数を増やしました。中古で数万円ほどの安価なパソコンでしたが、サクサク動くものを選び、『パソコンを使えば便利でわかりやすい』ということを実感してもらいました。その後、現場にも導入しました。シンプルなスケジュール管理ツールを入れて、計画の並び替えなどを私が実演しながら、パソコンの便利さをアピールしました。
ーーまずはパソコンが便利であることを知ってもらうことから始まったのですね。
それまでパソコンなしで仕事をしてきた人の立場になると、なくても仕事できるよと思うのは考えてみれば当然なんですよね。ですので、例えば「こっちを更新すれば、向こうのパソコンの情報も更新されますよ」というようなところから丁寧に説明して、便利さをわかってもらう必要があると思ったんです。
ーー確かに、「面倒だし、わからないから必要ない」と言われてしまったらそれまでですよね。
最初の方は「やっぱりわかんねぇなぁ・・・」と言われたこともありました。でも、根気強く必死にパソコンの便利さを伝え続けていると、少しずつ便利さをわかってくれる人が増えてきました。
ーーどのくらいの時間をかけて進めていきましたか?
2年くらいかけて少しずつパソコンの台数を増やしていきました。パソコンは最新機器である必要はなく、工場内で使うことを考慮して、中古の安価なものを選びました。
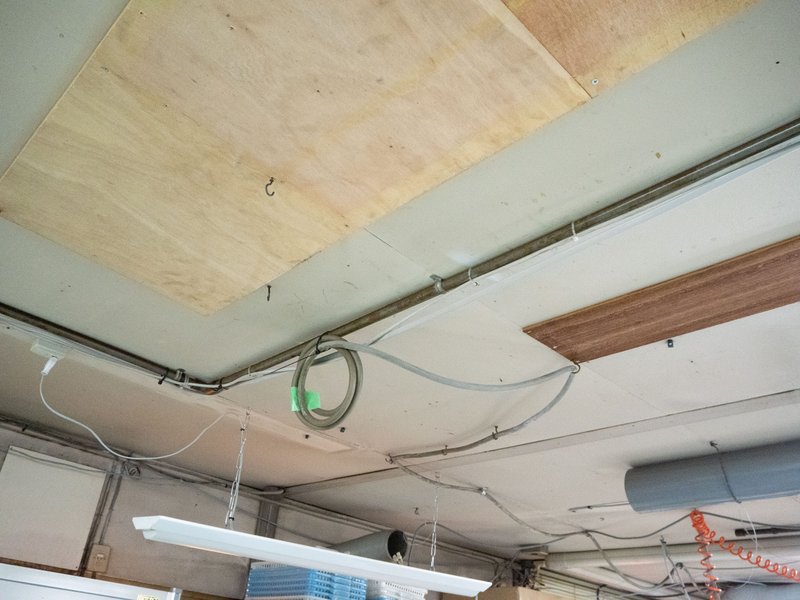
ーーネットワークなどの整備も今村さんが行なったのですか?
はい。自分でLANケーブルを工場に張り巡らせました。見栄えは良くないですが、機械が発する電波のノイズ干渉があったため、無線ではなく有線で繋いでいます。以前の会社を思い出しながら全部自分でセッティングしました。
ーーすごく大変だったと思うのですが、そのモチベーションはどこにありましたか?
「ここが潰れたら終わりや」と思い必死でした。今村精工を残していくために、間接的な無駄を省く必要があり、それにはデジタル化により情報を見えるようにすることが必須だとわかっていたのでやるしかなかったです。
シンプルな管理ツールで更に見える化

ーースケジュール管理ツールを使ったことで、どんな効果がありましたか?
工程ごとの予定や、いつ頃どんな加工が自分の工程に来るのかなどをモニターに表示させたことで情報把握がスムーズになりました。多くの会社さんがホワイトボードに工程表を書くのをそのまま電子化したイメージです。効果があった反面、事務所と工場で情報が連動しない問題もありました。パソコンやネットワークが工場に浸透するに従って、もっと管理できるツールが欲しくなり、『ものレボ』という工程管理ツールを導入することにしました。
『ものレボ』とは、製造業専門のクラウドアプリケーション。特に、「少量多品種」で「短納期」の製造業向きの工程管理ツール。
工場DXならMonoRevo(ものレボ) - 工程管理を無料で始められるクラウドアプリ製造業専門のクラウドアプリケーションのMonoRevo(ものレボ)なら、かんたん操作で工場の製造工程のすべてを見える化。工monorevo.jp
ーー『ものレボ』はどんなきっかけで知りましたか?
インターネットで工程管理ツールを検索していて見つけました。すぐに資料請求してデモを見てすぐに導入を決めました。
ーー決め手は何でしたか?
まずシンプルである点です。メモなどが自由に書き込めるツールだと、自分以外の人が書いた内容がわからなくなってしまう時があります。そのため、できることが決まっているようなシンプルなツールであることは最優先でした。更に、会社のネットワーク以外からもアクセスできる点や、『誰かが開くと他が開けない』ということがない点も弊社に合っていると思いました。
ーー実際にどのような場面でツールを使っていますか?
受注後まずは、事務所で基本的な納期や図面などの情報をものレボに登録します。次に、登録した際に発行された番号と図面が現場に渡ります。そして最後に、現場のメンバーがそれぞれの工程を組み立てて登録するという流れです。
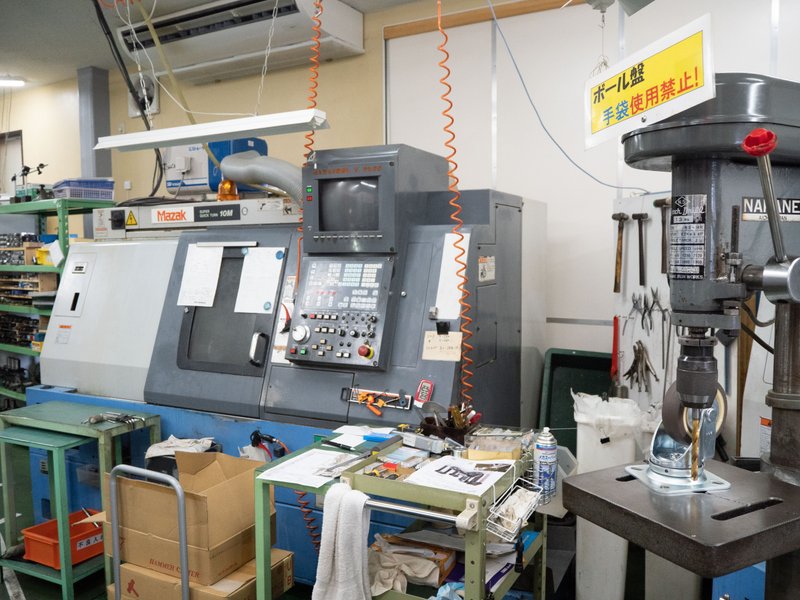
ーー現場で工程を組み立てるのは、どなたかリーダーや工場長の方がされるのですか?
弊社では機械の担当者が工程を組み立てているため、それぞれが自分の工程を自分で登録しています。機械1台に対して担当者1人というような形になっていて、機械がいつ空くのかという管理も個人に任せています。
ーー予定に対する実績状況は記録していますか?
はじめは作業後に実績登録をしていたのですが、そこまでやると現場の負担が大きくなってしまい、今は記録していません。今もちろん実績のデータは取りたいですが、合わないことは無理してやらず、とにかく少しでもツールに触れて慣れてもらうことを優先しています。
ーー『ものレボ』は主にパソコンから情報を見ているのですか?
社員はほとんど1人1台パソコンがあるため、それぞれの機械の横に設置してあるパソコンからログインしています。現場にはタブレットも数台用意してあるので、それで情報をチェックしている方もいます。
ーー『ものレボ』を導入してどんな効果を感じていますか?
特に、弊社で後工程と呼ばれる製品の仕上げや検査をする担当の方々が、「いつ製品が来るのか把握しやすくなった」と言ってくれています。製品ごとの予定を見ることができるので、いつ終わるのか現場に聞きに行くことが格段に減りました。
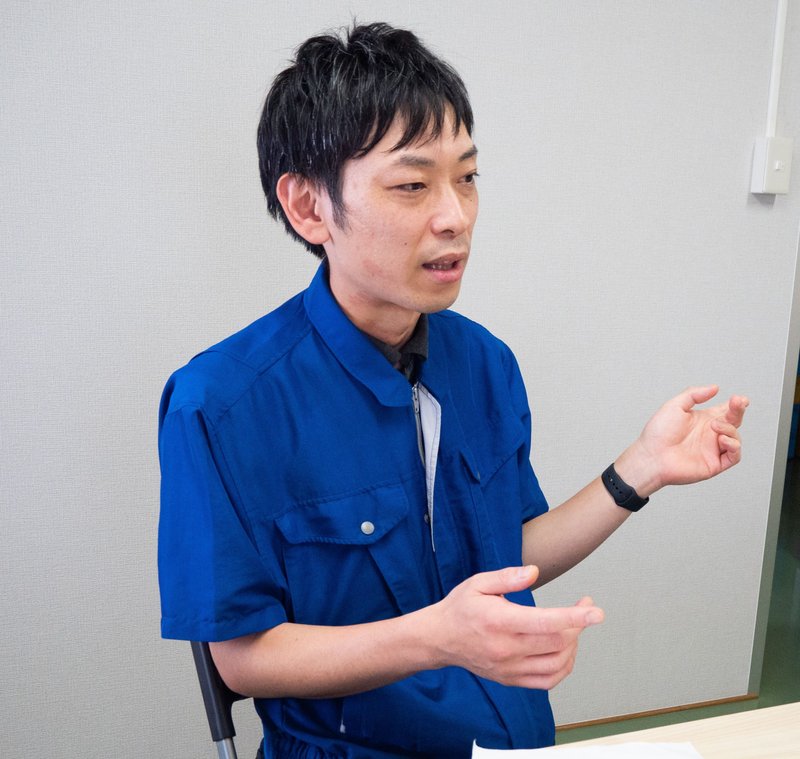
ーー現場で機械加工をされている方はどうですか?
現場で働くひとりひとりにメリットがあるかと言われると、もしかすると今の段階では全員がメリットを実感できていないかもしれません。でも、全体として管理ができているため、問い合わせやトラブルへの対応は早くなり、結果的には現場にもメリットはあると考えています。
ーー例えば、加工時間を10時間と予定を立てて開始してから、15時間に変更となった場合はどのように管理していますか?
予定が始まってしまうと調整が難しくなってしまいます。厳密に言えばできるのですが、ややこしいことになってしまうため、その時はものレボ上の予定はそのままにして、次工程と打ち合わせして調整しています。ちょっと使いづらいなと思うところは開発元に伝えています。
わかりやすく、伝わりやすくするためのツールも次々導入
ーー『ものレボ』の他にIT面で変えたことや工夫していることはありますか?
■図面はスキャンして保存
以前は紙の図面をそのまま保管していたため、探すのがかなり大変でした。図面をタブレットで見ながら加工したいとも考えましたが、加工しながら書き込んだり書き直したりするのでやっぱり紙の図面が便利なんです。書き込んだ図面も含めてスキャンして保存しておくことで、問い合わせの際に図面を探す手間が短縮され、再度同じ加工の依頼があった時にも役立ちます。
■スマホから確認できる温湿度計で管理
金属加工は気温や湿度が加工に影響を及ぼすため温度管理が重要なのですが、同じ工場内でも場所によって気温の差があり管理が難しかったんです。そこで、「SwitchBot温湿度計」を活用し、一定の温度を超えるとスマホに通知が来るように設定しました。現場で社用スマホを所持しているメンバーにも通知が来るようになっているため、温度や湿度を意識するようになりました。
■機械の稼働状況や検査室の空き状況をカメラで見える化
機械や検査室の様子を写すカメラを設置しました。最初は監視カメラみたいと言われましたが、使っていくうちにわざわざその場所へ行かずとも様子がわかるのがとても便利だと受け入れてくれるようになりました。
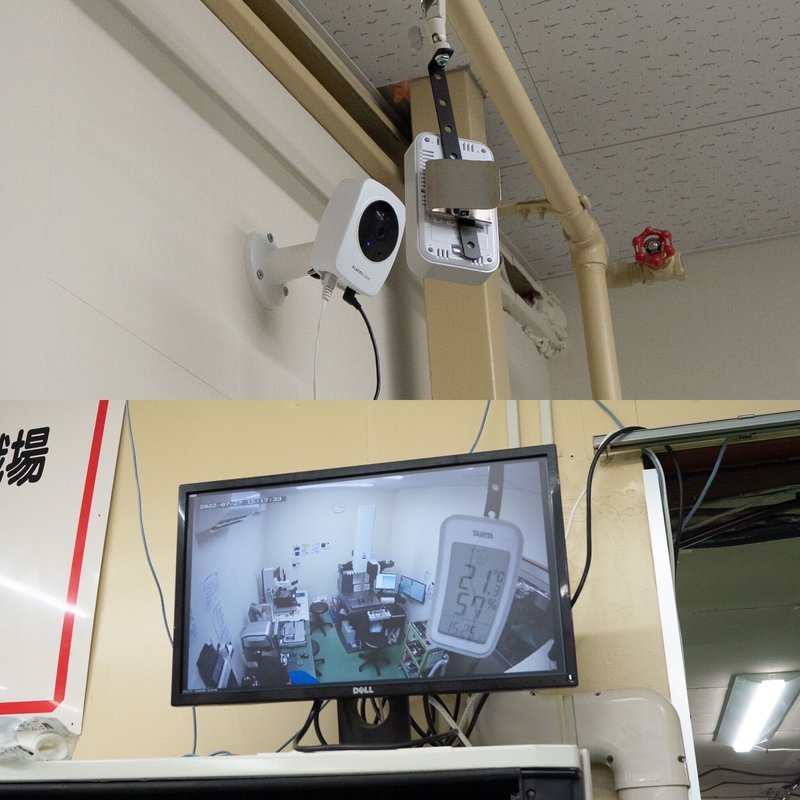
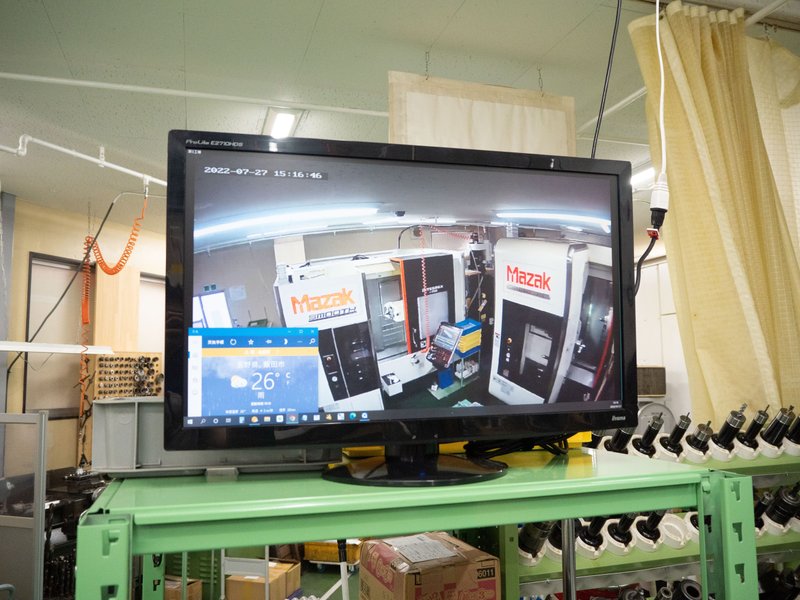
ーー便利なITツールやアイテムに関する情報はどうやって収集しているのですか?
私は自宅の中で使えるIoTツールとかスマート家電が好きなんです。妻が結構詳しくて、温湿度計は元々自宅で使っていました。使ってみて便利だったので工場にも導入したという流れです。カメラは子供が小さい頃に使っていた見守りカメラを応用しました。
ーーコミュニケーションツールなどは使っていますか?
ほぼ全員がLINE WORKSを使っています。人の手をできるだけ止めないようにするため、業務的なやり取りはLINE WORKSを使ってチャットで会話するようになりました。記録も残りますし、話すために人を探すこともなくなりました。LINE WORKSを使うようになって、もっと便利に活用するためスマホ導入を決めました。
ーーチャットはスマホの方が便利そうですね。
最初は1人1台パソコンがあるから大丈夫だろうと思っていましたが、結局パソコンのところに行かないと見ることができません。スマホがあればチャットはもちろん音声通話もできますし、写真撮影もできます。そして更に最近スマートウォッチも導入しました。
ーースマートウォッチですか。
スマホはすごく便利ですが、加工中に手が汚れていると操作できません。連絡が来たと思って急いで手を洗って確認すると、後から見ても問題ないような連絡だったということが多々ありました。現場のメンバーも同じことを感じていたのでスマートウォッチはすごく好評でした。私自身が現場で加工していて不便だなと思ったことは一つ一つ改善策を考えています。
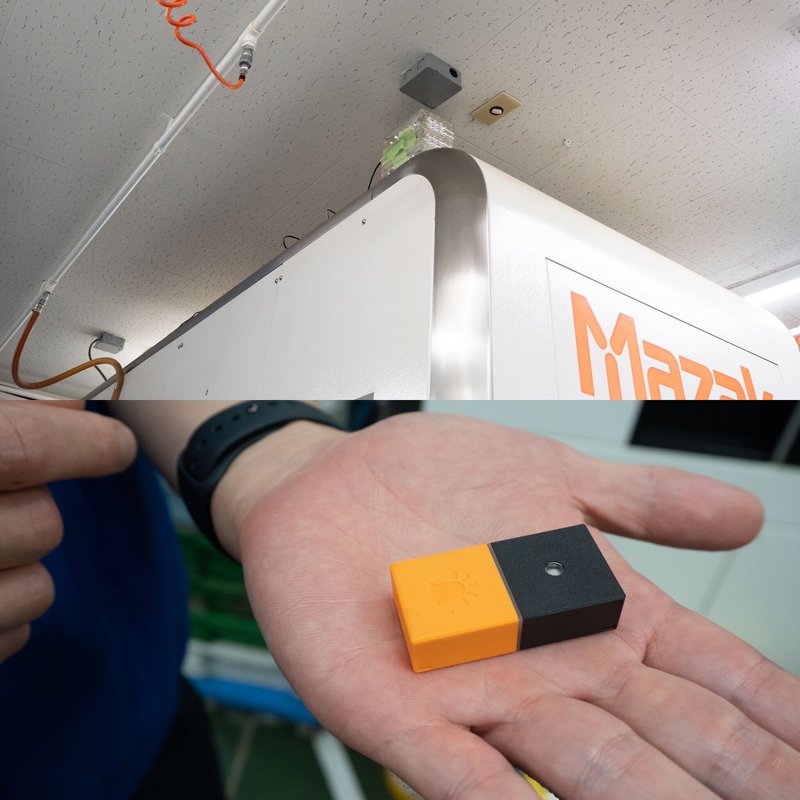
ーー今村さんご自身が感じている不便さをご自身で改善されているのですね。
もっと作業に集中するために、もっと便利にもっと楽にしたいと思っています。この時代、中古でも安価でも性能の良いデバイスが手に入るので、仕事で使えそうだと思ったものは積極的に使いたいです。便利なアイテムを導入することはもちろんですが、パソコンやスマホ渡したらそれで終わりではなく、使う立場になって考えることが大事だなと実感しました。
小さなロスをなくして、仕事に集中!
ーーこれから使ってみたいITツールやアイテムなどはありますか?
小さなロスをなくすという視点から、電子タグによる工具管理に取り組みたいと思っています。現在、検査に使用する道具はホワイトボードに日付と使用者を記入しているのですが、その場に行かないと貸出中かどうかは確認できません。検査具に電子ダグを付けて、持ち出したら自動で記録されるような仕組みができないかと考えています。
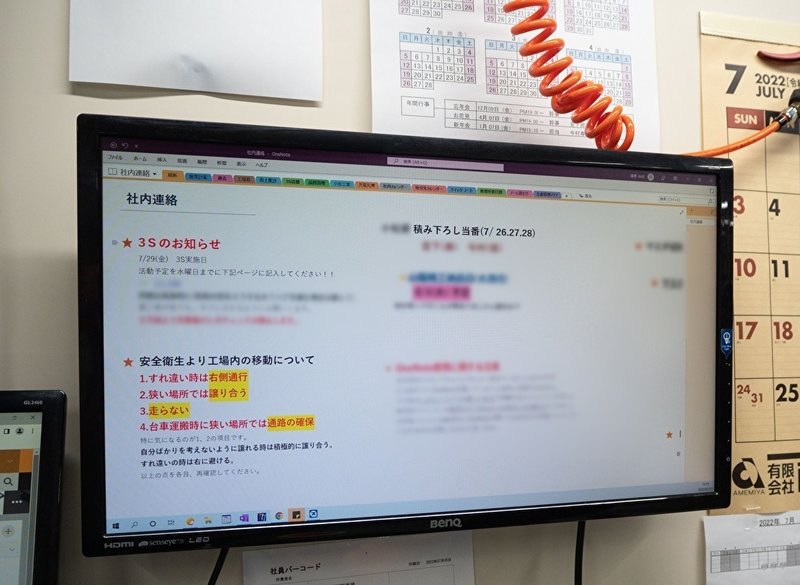
ーー小さなことですが、グッと便利になりますね。
ちょっとしたことでも間接的な作業を潰していき、作業に集中したいです。その積み重ねが、将来に繋がると考えています。
ーー社長であるお父様から何かコメントはありましたか?
約10年間私がやってきたことに対して、否定的なコメントはなく協力してもらえています。徐々に売上が上がったという成果が出たことも大きいと思います。
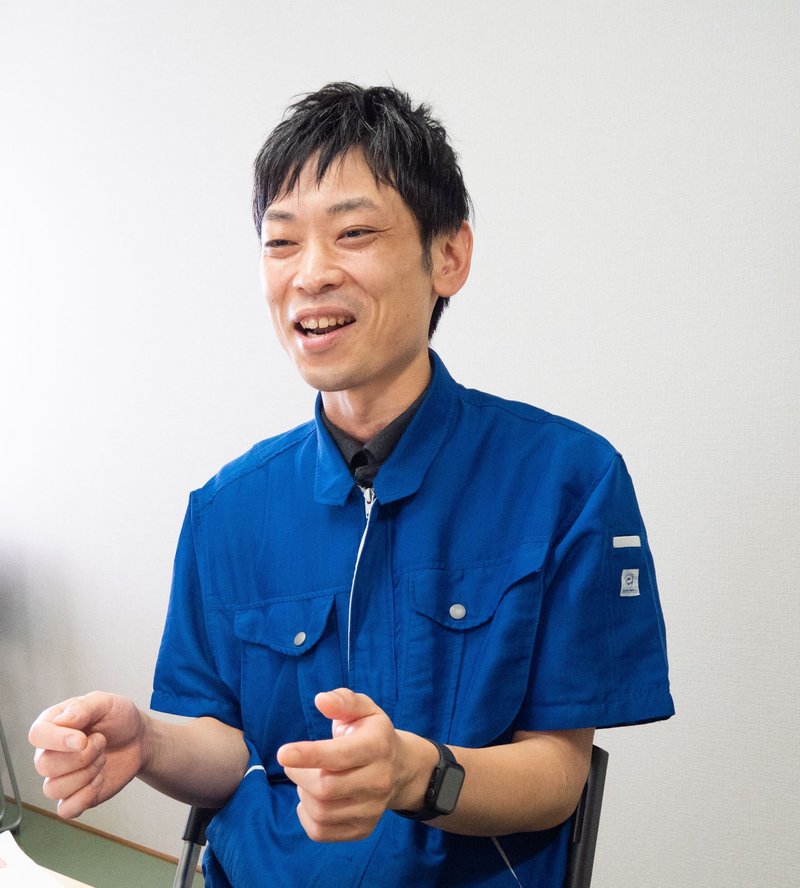
ーー今村さんの目標を教えてください。
現在私が担当している機械は私1人しか担当者がいません。やはり早く私以外にも扱える人を育てて、経営などにも本格的に携わり、会社を継ぐことを考えていきたいと思っています。職場環境に関しては、女性が働きやすい職場にしたいんです。
ーーどのような背景からそう思われたのですか?
今は男性中心の職場ですが、女性でも働ける職場にして男女問わず働きやすい会社にしていきたいです。現在産休に入っている社員がいるのですが、今村精工にとっては初めてのことです。いろいろなことを便利にしていくと同時に、勤務時間なども働きやすいように変えて長く働ける職場にしたいです。
次に、実際に今村精工で働いている社員の方にインタビューしました。今村さんがIT・IoT化を進めている工場で働く方は、この環境の変化をどう感じているのでしょうか?
品質管理 冨永美穂(とみなが みほ)さん
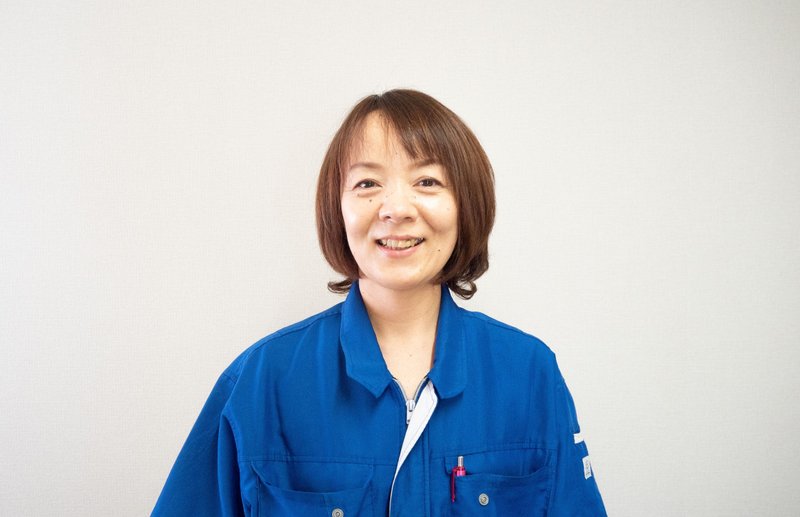
ーー今村精工に入社したきっかけを教えてください。
実はものづくりに興味があったわけではなく、通勤距離など条件面でいいなと思ったので事務職の求人に応募しました。ものづくりは全く経験がありませんでした。
ーー事務職ですと、現場でのものづくりには直接関わることはなかったのでしょうか?
それが、入社してすぐに「現場の仕事をやってみてほしい」と言われました。事務として入社しましたが、最初の方は現場でマシニングセンタを使って加工していました。
ーーそうだったのですね。現場での仕事はいかがでしたか?
特に抵抗もなかったですね。自分がセットした材料が削れていくのを見ると面白いなと思いました。現場を経験した後に事務の仕事をしました。
ーー現場のご経験があるということは、現場の方が使っている専門用語がお分かりになるということでしょうか。
ある程度のことはわかりますね。こんなこと言ってるのかなとイメージすることはできます。
IT・IoT化 最初は「私にできるのかな・・・」
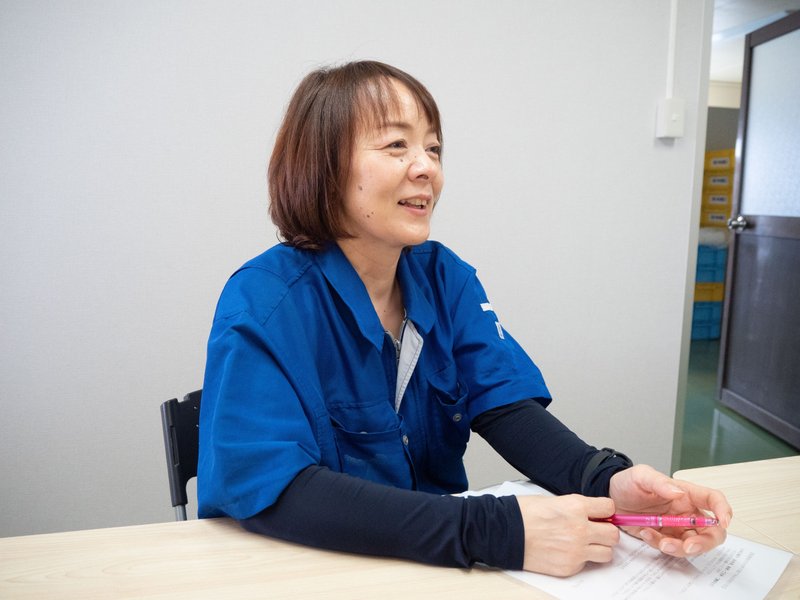
ーー10年前に今村さんが入社されて、IT・IoT化されていく会社を見てきていかがですか?
最初は難しそうで「私、これできるのかな」なんて思っていました。でもやってみると、なんで今までやってこなかったんだろう!と思うくらい便利になりました。
ーー具体的にはどんな効果を感じましたか?
事務所からでも現場の様子がわかるというのが一番良かったです。メッキ処理や仕上げなどの後工程は私が予定を立てているのですが、現場での加工が終わるのがいつ頃かわからなくて、事務所から出て現場に聞きに行っていたんです。それが、工程管理ツールを見ればおおよその日程がわかるのでとても便利になりました。
ーー知りたい情報は事務所内でほとんどわかるのですか?
基本的な日程はほとんど把握できるようになりました。急な変更があった場合などは把握できないこともあります。でも、「変更があったら教えてほしい」と現場に伝えているので、以前よりもコミュニケーションがスムーズになったと感じています。変更の内容はLINE WORKSで送ってくれることもあるので、文字に残るしいつでも連絡が取れて便利ですね。
ーーどんどん新しいツールやアイテムが導入されていくのはどうですか?
最初の頃は、「便利なら使ってみたいけど覚えられるかなぁ」と躊躇していましたが、今はもう「やるっていうなら、やる!」と腹を括った感じです。笑 色々経験したおかげで、最初だけ頑張って覚えればなんとかなるなとわかりました。

ーー今までやってみて便利になっている実感があるからこそ、前向きに捉えられるのですね。
そうですね。中には前の方が良かったなぁという人もいるんですが、そんな時は「でもこれからの時代、それじゃダメだよね」と声を掛けてやってもらうように働きかけることもあります。
ーー今村さんにとって富永さんからのその一言は心強いと思います。
私は今村精工で20年以上働いているので、みんな話を聞いてくれるのだと思います。笑
ーーこの先どんな会社にしていきたいですか?
IT・IoT化していくことは会社として良い方向に向かっていると感じます。今後、若い世代が入ってくる時も取っ付きやすいと思いますし、これからも積極的に活用していきたいと思います。
現場で働いているメンバーを見ていると、工程管理ツールへの入力などは正直大変そうだなと思うこともあります。入力している時間も取れないくらい機械を動かさなければいけないこともあります。でも、今まで誰がどんな仕事をしているか知らずに仕事をしていたと思うんです。共有することによって自分以外の人の仕事を知ることができたというのも意味があることだと感じます。
ーー今後取り組んでいきたい仕事などはありますか?
人を育てることに力を入れていきたいです。改善のおかげで仕事が少しずつ楽になってきた実感はありますが、そもそも私が抱えている仕事が結構あり、その負担が大きくなっています。技術者も含めて、新しい人材を育てていくことも取り組んでいきたいです。
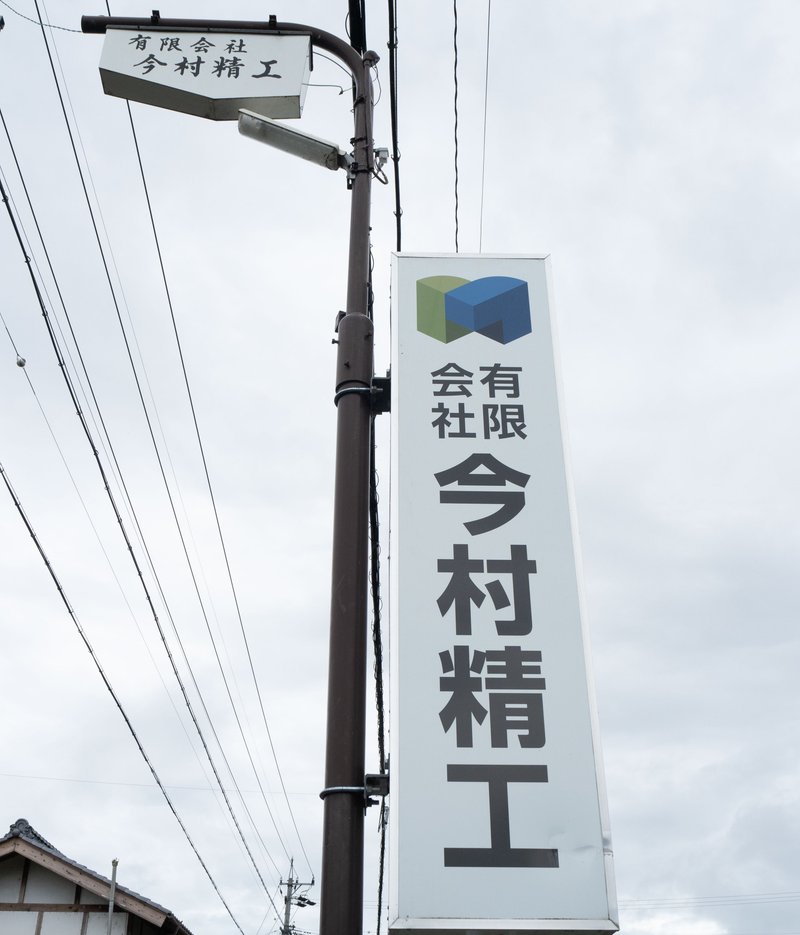
ーあとがきー
工場のIT・IoTを進める今村清孝さん、そして、その工場で働く冨永美穂さんにお話をお伺いしました。元金型メーカーに勤務していた筆者が『工場のIT・IoT化』という話題について取材する際、気になるのが現場の大きな負担にならないかということです。
現場側の手間を一切かけずに管理するのは不可能だとしても、入力方法が複雑すぎるものは、必要以上に現場の負担が大きくなってしまいます。管理することでどんなメリットがあるのか、現場側がその効果を感じられない場合も、ただ負担が増えただけとなってしまう可能性があります。
こうすれば良いという画期的な方法はないかもしれませんが、今村さんのように『現場でパソコンを使う便利さ』を感じてもらうことから始めるやり方は効果的だと感じました。